Final Design Modification Process
The final design modified to make it realistically manufacturable given COVID-19 restrictions.
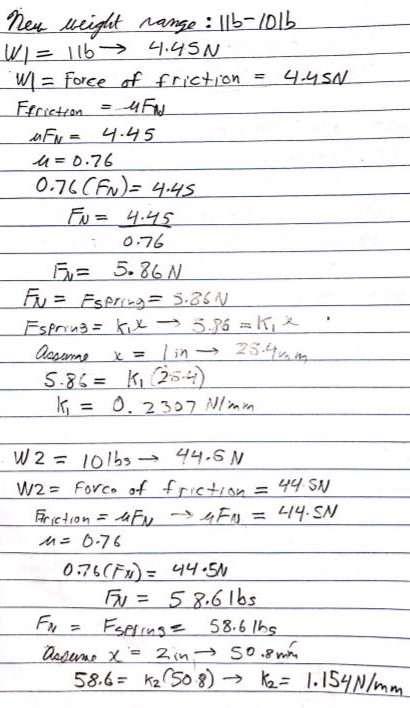
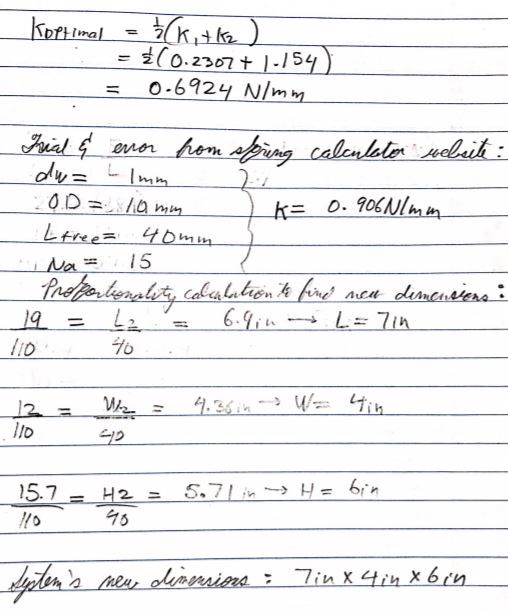
Calculations to scale down the entire system were done by determining the spring dimensions necessary to hold our testing weight scaled down from 250 lbs to 10 lbs. Then, using proportions, the outer casing was scaled down and the interior components scaled down to fit the new sized case.
These values were used as a starting point, and slightly modified as additional parts were removed to ease the manufacturing and assembling process.
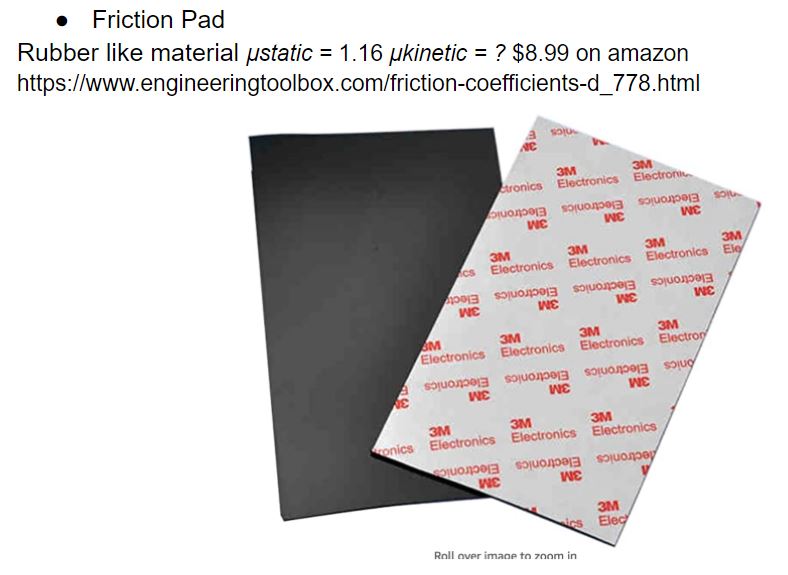
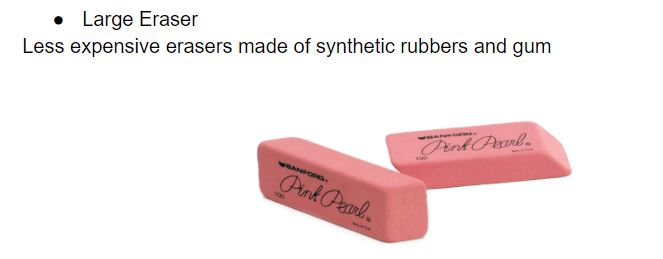
Since our system will be scaled down, we will be purchasing a much smaller brake pad material than initially decided during our design phase. We considered a variety of inexpensive rubber options and chose friction pads as our final option.
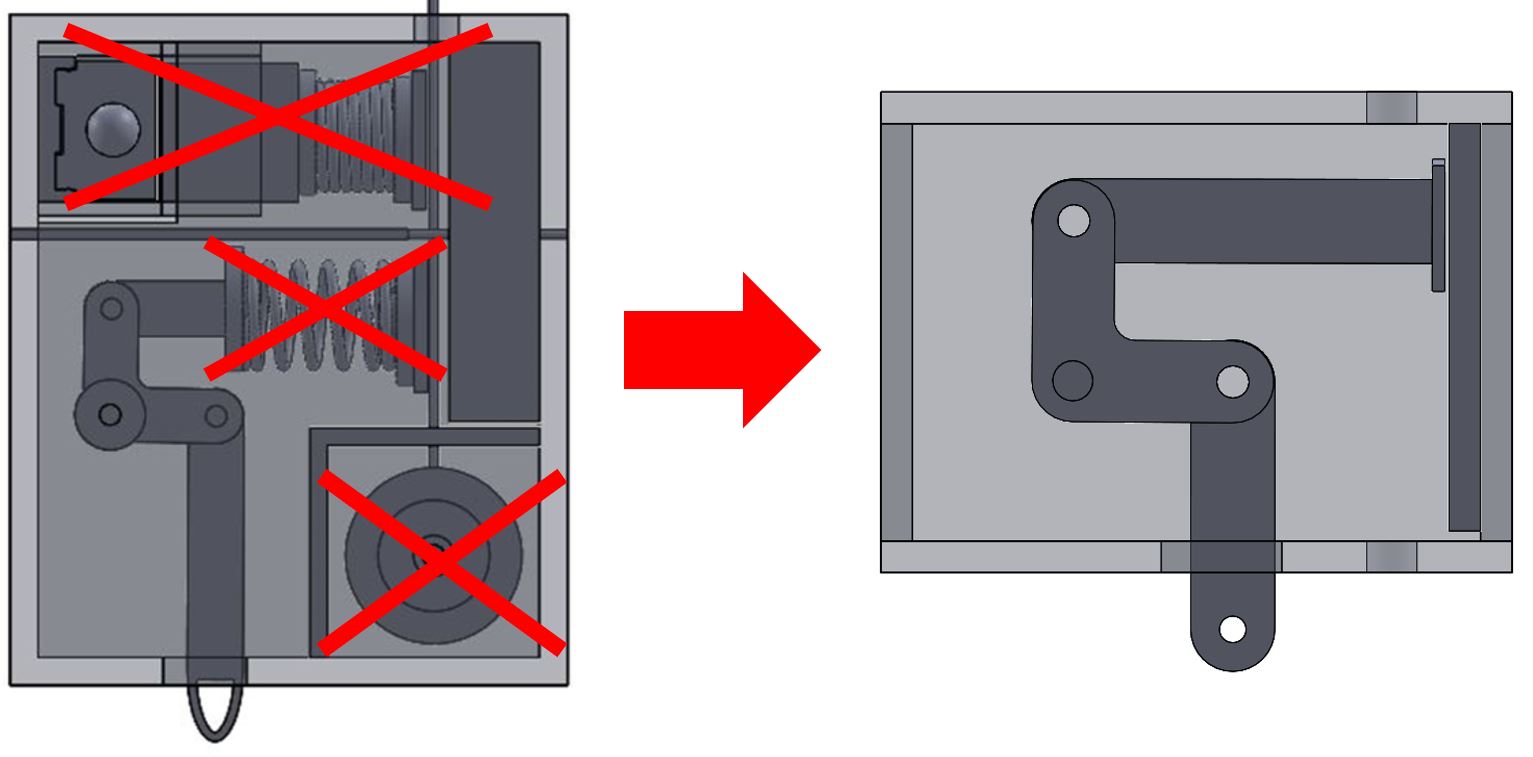
The CAD model was updated to reflect our changes. We decided to remove the hard brake system because the revised system was light enough that we could hold the rope in place on our own without the need of a hard brake. We also removed the spring in the lever arm as we realized that a solid arm is enough to transmit force to the brake pads, and adding a spring will complicate the design. Finally, we removed the spool as the length of the rope is short enough with the modified design to not need a spool.