Manufacturing Plans
Figuring out how to manufacture our parts.
We will be purchasing many of the parts to ensure part integrity without needing to test for requirements ourselves. Some will be modified to perform functions specific to our design.
Other parts will have to be custom manufactured.
The most critical part we will be manufacturing is the bell crank lever. It requires tight tolerances as the friction on the rope depends largely on the travel of the lever.
The design of the lever will be evaluated using SolidWorks Simulation to ensure it meets our design requirements. Once the design is confirmed, we will purchase an aluminum stock that is big enough for the lever to be made out of. The Computer Aided Manufacturing feature will be used to generate G codes for the CNC machine to perform milling operations.
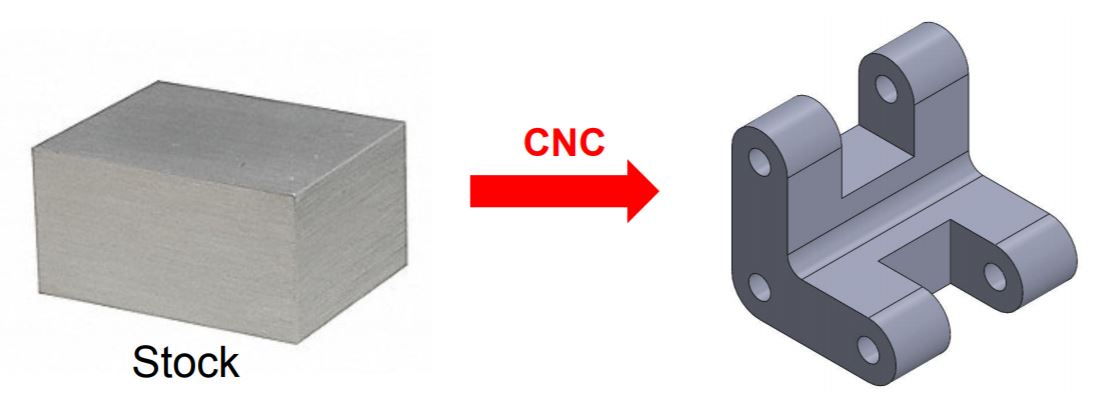
Another important part that needs to be machined is the housing. The housing serves not only as an enclosure but also as a structural frame that many parts rely on to operate. The housing could be made out of metal to provide structural integrity. Therefore, we might need to weld the housing together.
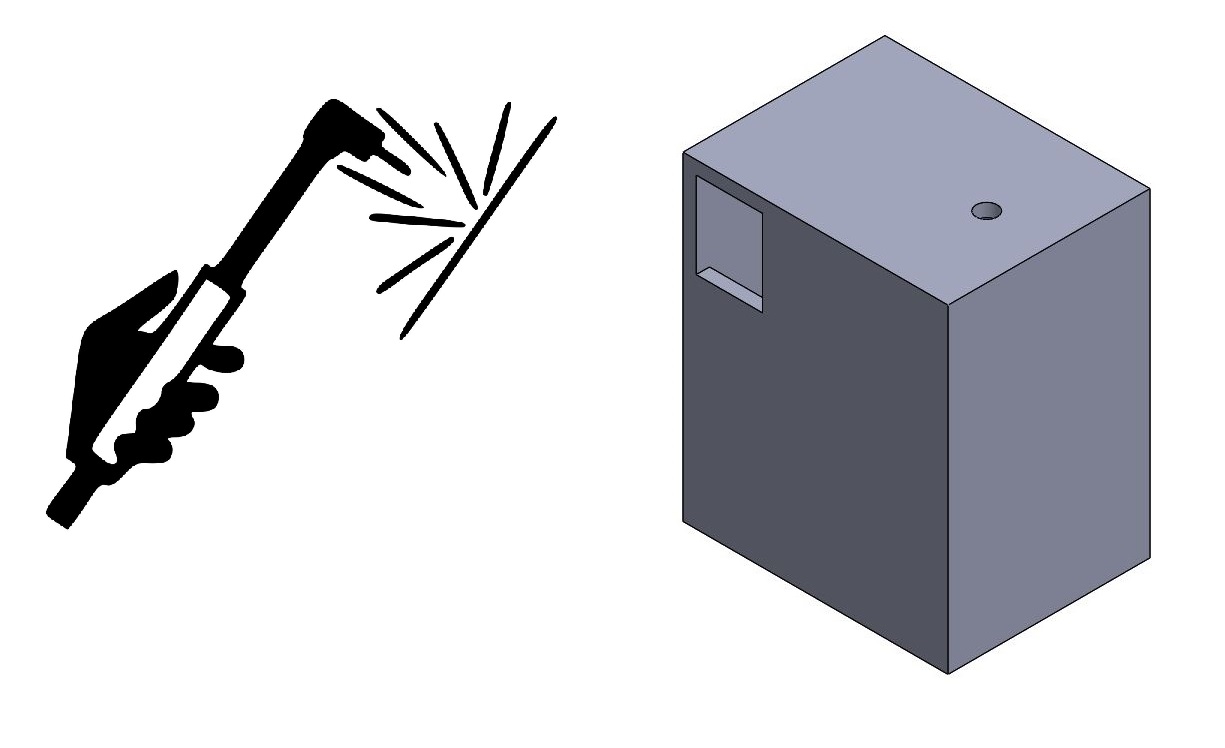
The parts that require machining are going to be manufactured using the CNC milling machine. We can use the CNC machine at Grove School of Engineering to machine the lever and other parts. This means that the rest of the parts can be either purchased or fabricated in our house to minimize the cost.
We need to consider using lightweight and high strength material like aluminum to achieve as much portability as possible. However, certain parts may need to be made out of steel depending on the analysis on the strength requirement. For example, the pins that connect the lever and the arms as well as the hinge could require to be made out of steel.
The estimated build time is 8 weeks. The components in the active braking system, modification of purchased parts and the housing will take 2 weeks each. We will use another two weeks as back up to fine tune or trouble shoot other unanticipated problems that arise during the final stage of the assembly.
There will be very little to no cost on the labor of machining the parts. One of our team members is a machine shop technician and has access to CNC machines as well as welding machines in our school.